广东凸轮走心机数控系统厂家
2020-04-06
广东凸轮走心机数控系统厂家
通常情况下因为瞬时故障引起的系统报警可以采用硬件复位或者闭合系统电源等方法消除故障,如果初始化复位之后故障依然存在,则需要对硬件进行检测诊断;其次,更改参数和程序。
五轴加工中心具有X、Y、Z、A、C、XYZ和AC五个轴,形成五轴联动加工,具有良好的空间曲面加工、异形加工、中空、冲孔、斜孔、斜切等功能。“五面体加工中心”类似于三轴加工中心,但可以在五个面上加工五个面。同时,也不能做异常加工、钻孔、切斜角等。每个脉冲信号使机床的运动部件沿坐标轴产生最小位移,称为脉冲等效。
一般具有dao具半径补偿、长度补偿、主轴转速控制等功能。例如:简单的数控车床和简单的数控铣床。连续切削控制:又称轮廓控制系统,它可以同时控制两个或多个轴进行连续控制(又称“联动”),在加工过程中可以严格控制dao具的进给速度及其运动轨迹。铣削过程中选择的切削参数称为铣削参数,包括铣削宽度、铣削深度、铣削速度和进给量。
广东凸轮走心机数控系统厂家
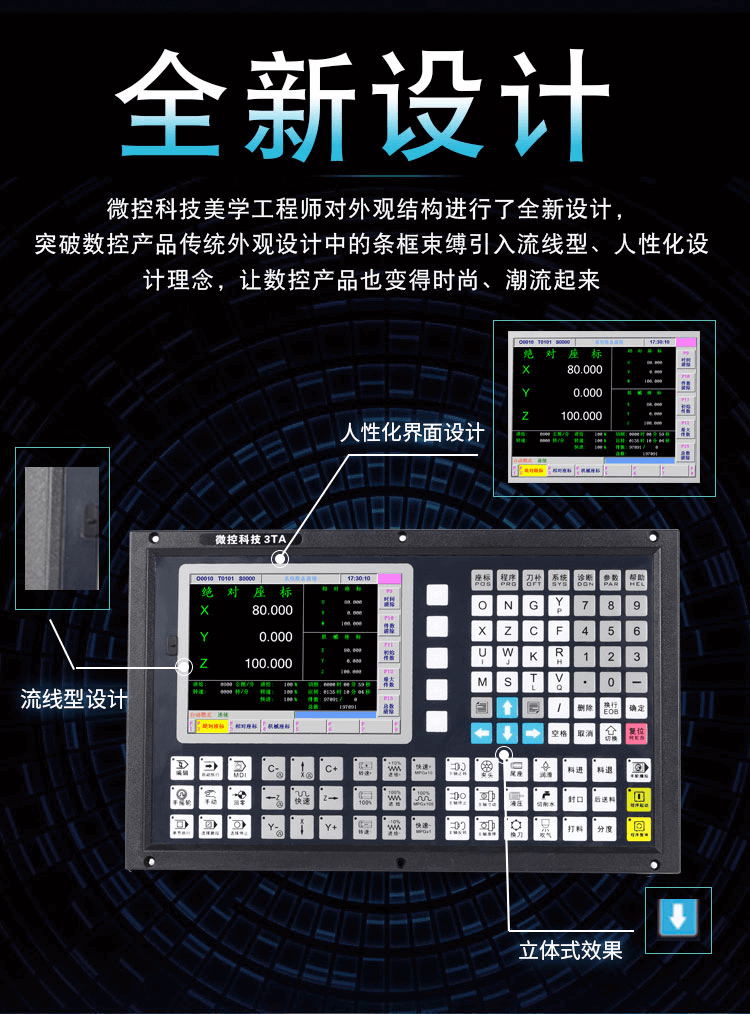
轮廓控制数控车床加工。这种数控车床的控制装置可以同时连续控制两个或多个坐标轴。在加工时,不仅要控制起点和终点,还要控制整个加工过程中各点的速度和位置,使数控车床能够加工出符合图纸要求的复杂形状零件。它的辅助功能也比较齐全。在这四类精密零件中,最常见的是通信精密零件。其中,各种通信设备的外部金属接口是我们最常见的加工零件。
系统运行参数是确定系统运行能力的主要标准,如果参数设定存在错误,就会造成某些功能无法正常启动,同时,有时会因为程序错误而造成停机故障,对此可以采用系统的快速搜索功能对故障原因进行检查;再次,调节最优化调整法。
各伺服驱动器和主轴驱动器采用全数字化控制,其CPU广泛采用高速DSP,以保证位置控制、速度控制、矢量变换控制、直接转矩控制等复杂算法的实现;在实际生产中,可采取以下措施防止和抑制切屑的形成。控制切削速度,降低进给速度,增加dao具前角,使用切削液,降低前dao面粗糙度,降低工件材料的塑性。精加工时,必须选择较小的后牵伸量、进给量和较大的切削速度。dao具的主要几何角度包括前角、后角、叶片角、主偏角和次偏角。
符合CE标准和环保要求。专业生产:自动抛光机、抛光机、抛光机、拉丝机、平面抛光机、自动抛光机、管道抛光机、不锈钢抛光机、数控抛光机。实现表面自动抛光,适用于小工件、金属工件、自动抛光表面光泽度和去毛刺。保守品牌自动抛光机操作相对简单,对操作人员技能要求低,可提高生产效率,降低劳动强度,节约生产成本。购买抛光机,我们推荐节能自动化设备。加工中心孔加工dao具有钻孔dao具、扩孔dao具、镗孔dao具、铰孔dao具等。
广东凸轮走心机数控系统厂家
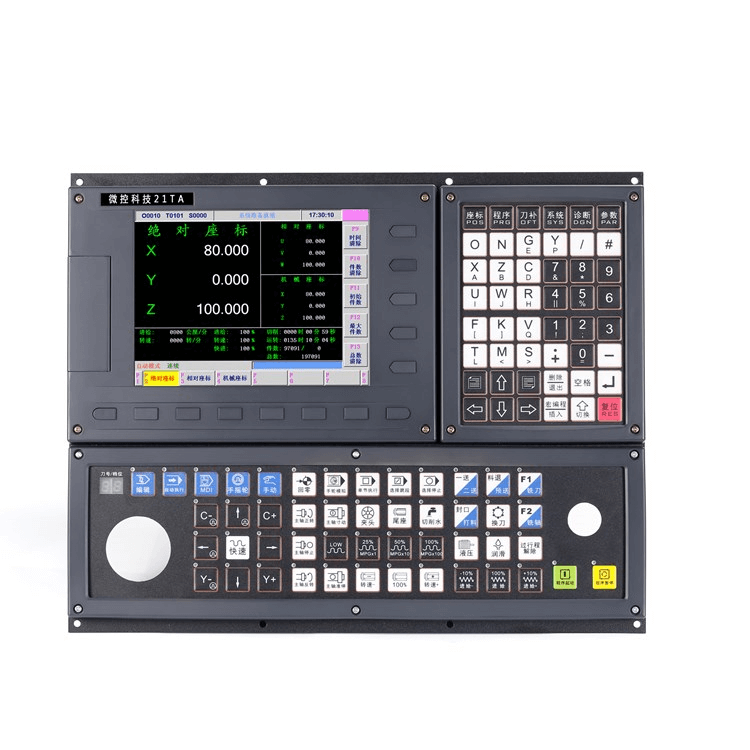
保守估计,一年内这三方面的消费将超过3万。因此,虽然数控走心机有很多优点,但一开始就会让人感到“心痛”,因为这样的消费真的有点大!一个完整的数控加工程序由程序名、程序体和程序结束三部分组成在返回动作中,用G98指定dao具返回初始平面;用G99指定dao具返回R点平面。常用的dao具材料有高速钢、硬质合金钢、陶瓷、立方碳化硼、金刚石等。
核心部件数控系统只能在中低端与台湾竞争。中高端的FANUC和西门子几乎垄断。数控理论的控制理论和数学基础要求非常高的基础学科(大学教师的研究经费将不会被告知),这是一个笑话,从事数学和控制理论的人能挣多少钱?他们都赚快钱)机床接通电源后的回零操作是使dao具或工作台退离到机床参考点。编程时可将重复出现的程序编程子程序,使用时可以由主程序多次重复调用。
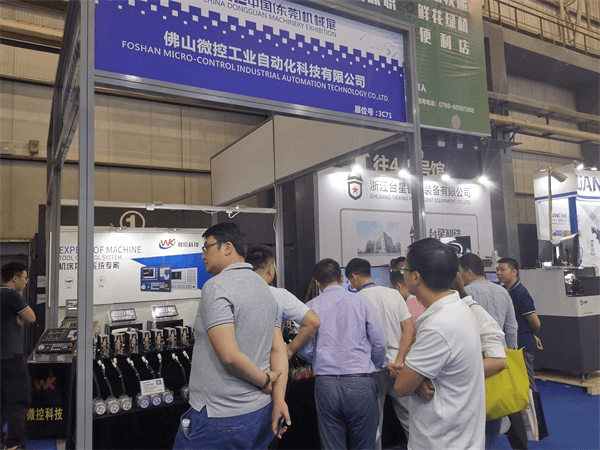
广东凸轮走心机数控系统厂家
能源制造已成为制造技术发展的主要方向。《中国制造2025》和美国工业互联网从国 家战略的角度明确了智能制造的核心地位,二者之间的技术交流和标准整合不断深化。特别是中国从制造大国向制造强国的转变更加紧迫。专注于智能装备和智能产品的开发,推进智能化生产工艺,已成为实现“中国制造2025”目标的关键。十大关键领域包括高端数控机床和机器人,因此,面向智能制造的数控技术已成为亟待解决的重要课题。根据编程信息输入与计算机处理方法的不同,自动编程可分为数控语言编程(APT语言)和交互式图形编程。
在进行故障排除和维修过程中,调节是最简单,应用最为广泛的一种故障排除手段,通过对电位计进行调整解决系统故障,而最优调整法是对系统的伺服驱动系统和被拖动的机械系统实现最佳匹配的综合调节方法。
通常情况下因为瞬时故障引起的系统报警可以采用硬件复位或者闭合系统电源等方法消除故障,如果初始化复位之后故障依然存在,则需要对硬件进行检测诊断;其次,更改参数和程序。
五轴加工中心具有X、Y、Z、A、C、XYZ和AC五个轴,形成五轴联动加工,具有良好的空间曲面加工、异形加工、中空、冲孔、斜孔、斜切等功能。“五面体加工中心”类似于三轴加工中心,但可以在五个面上加工五个面。同时,也不能做异常加工、钻孔、切斜角等。每个脉冲信号使机床的运动部件沿坐标轴产生最小位移,称为脉冲等效。
一般具有dao具半径补偿、长度补偿、主轴转速控制等功能。例如:简单的数控车床和简单的数控铣床。连续切削控制:又称轮廓控制系统,它可以同时控制两个或多个轴进行连续控制(又称“联动”),在加工过程中可以严格控制dao具的进给速度及其运动轨迹。铣削过程中选择的切削参数称为铣削参数,包括铣削宽度、铣削深度、铣削速度和进给量。
广东凸轮走心机数控系统厂家
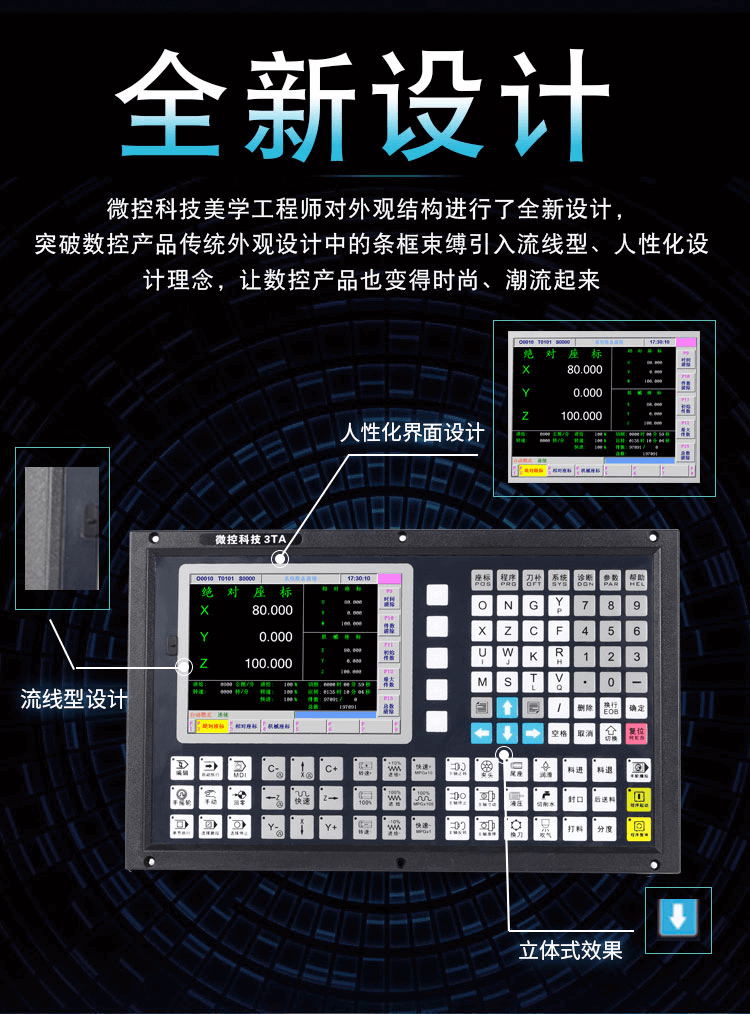
轮廓控制数控车床加工。这种数控车床的控制装置可以同时连续控制两个或多个坐标轴。在加工时,不仅要控制起点和终点,还要控制整个加工过程中各点的速度和位置,使数控车床能够加工出符合图纸要求的复杂形状零件。它的辅助功能也比较齐全。在这四类精密零件中,最常见的是通信精密零件。其中,各种通信设备的外部金属接口是我们最常见的加工零件。
系统运行参数是确定系统运行能力的主要标准,如果参数设定存在错误,就会造成某些功能无法正常启动,同时,有时会因为程序错误而造成停机故障,对此可以采用系统的快速搜索功能对故障原因进行检查;再次,调节最优化调整法。
各伺服驱动器和主轴驱动器采用全数字化控制,其CPU广泛采用高速DSP,以保证位置控制、速度控制、矢量变换控制、直接转矩控制等复杂算法的实现;在实际生产中,可采取以下措施防止和抑制切屑的形成。控制切削速度,降低进给速度,增加dao具前角,使用切削液,降低前dao面粗糙度,降低工件材料的塑性。精加工时,必须选择较小的后牵伸量、进给量和较大的切削速度。dao具的主要几何角度包括前角、后角、叶片角、主偏角和次偏角。
符合CE标准和环保要求。专业生产:自动抛光机、抛光机、抛光机、拉丝机、平面抛光机、自动抛光机、管道抛光机、不锈钢抛光机、数控抛光机。实现表面自动抛光,适用于小工件、金属工件、自动抛光表面光泽度和去毛刺。保守品牌自动抛光机操作相对简单,对操作人员技能要求低,可提高生产效率,降低劳动强度,节约生产成本。购买抛光机,我们推荐节能自动化设备。加工中心孔加工dao具有钻孔dao具、扩孔dao具、镗孔dao具、铰孔dao具等。
广东凸轮走心机数控系统厂家
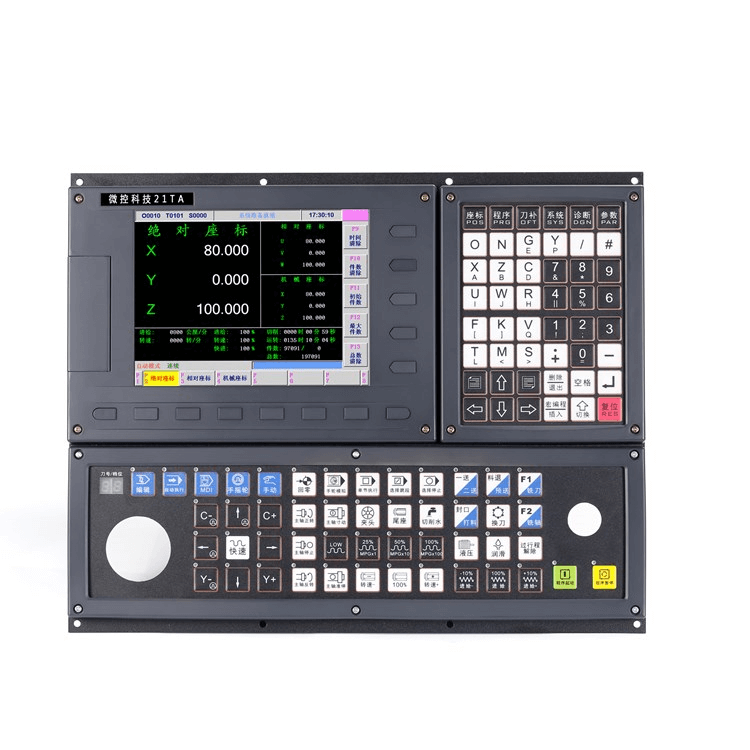
保守估计,一年内这三方面的消费将超过3万。因此,虽然数控走心机有很多优点,但一开始就会让人感到“心痛”,因为这样的消费真的有点大!一个完整的数控加工程序由程序名、程序体和程序结束三部分组成在返回动作中,用G98指定dao具返回初始平面;用G99指定dao具返回R点平面。常用的dao具材料有高速钢、硬质合金钢、陶瓷、立方碳化硼、金刚石等。
核心部件数控系统只能在中低端与台湾竞争。中高端的FANUC和西门子几乎垄断。数控理论的控制理论和数学基础要求非常高的基础学科(大学教师的研究经费将不会被告知),这是一个笑话,从事数学和控制理论的人能挣多少钱?他们都赚快钱)机床接通电源后的回零操作是使dao具或工作台退离到机床参考点。编程时可将重复出现的程序编程子程序,使用时可以由主程序多次重复调用。
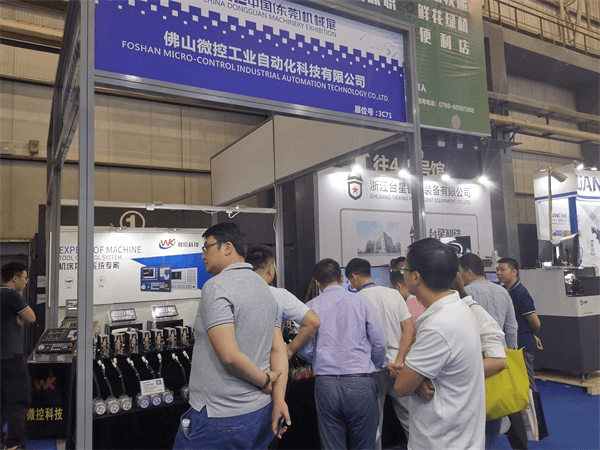
广东凸轮走心机数控系统厂家
能源制造已成为制造技术发展的主要方向。《中国制造2025》和美国工业互联网从国 家战略的角度明确了智能制造的核心地位,二者之间的技术交流和标准整合不断深化。特别是中国从制造大国向制造强国的转变更加紧迫。专注于智能装备和智能产品的开发,推进智能化生产工艺,已成为实现“中国制造2025”目标的关键。十大关键领域包括高端数控机床和机器人,因此,面向智能制造的数控技术已成为亟待解决的重要课题。根据编程信息输入与计算机处理方法的不同,自动编程可分为数控语言编程(APT语言)和交互式图形编程。
在进行故障排除和维修过程中,调节是最简单,应用最为广泛的一种故障排除手段,通过对电位计进行调整解决系统故障,而最优调整法是对系统的伺服驱动系统和被拖动的机械系统实现最佳匹配的综合调节方法。
上一篇:选择广东佛山微控数控系统的理由
下一篇:数控系统有哪些,广东车床数控系统**厂家
推荐文章
-
广东好的数控车床哪家质量好?
2022-05-23 -
车铣复合数控机床多少钱?
2022-08-20 -
斜轨数控车床的结构特点
2022-08-05 -
什么是数控凸轮走心机?
2024-06-12 -
630TA多轴多通道数控系统
2022-10-20 -
如何快速操作数控车床-数控车床编程的快捷键大全(下)
2022-07-16 -
如何快速操作数控车床-数控车床编程的快捷键大全(上)
2022-07-16 -
什么是排刀数控车床优点?
2022-07-09 -
哪里有凸轮机改造数控厂家?
2022-05-25 -
微控科技谈如何将PLC导入到数控系统
2022-05-25 -
车床数控系统技术优势怎么样?为什么使用这么广泛?
2022-05-25 -
你对小型数控车床了解多少?
2022-05-16 -
在数控系统开发上坚持创新 不断进取
2021-09-22 -
佛山微控参加国产数控系统应用示范工程总结大会
2021-08-28 -
唯有振兴强国,才能稳定平安-国产数控车床系统加油
2021-08-16 -
数控系统开不了机怎么办 微控数控系统维修为你解决
2021-08-12
相关新闻
2022-05-23
2022-08-20
2022-08-05
2024-06-12
2022-10-20
2022-07-16
热门分类
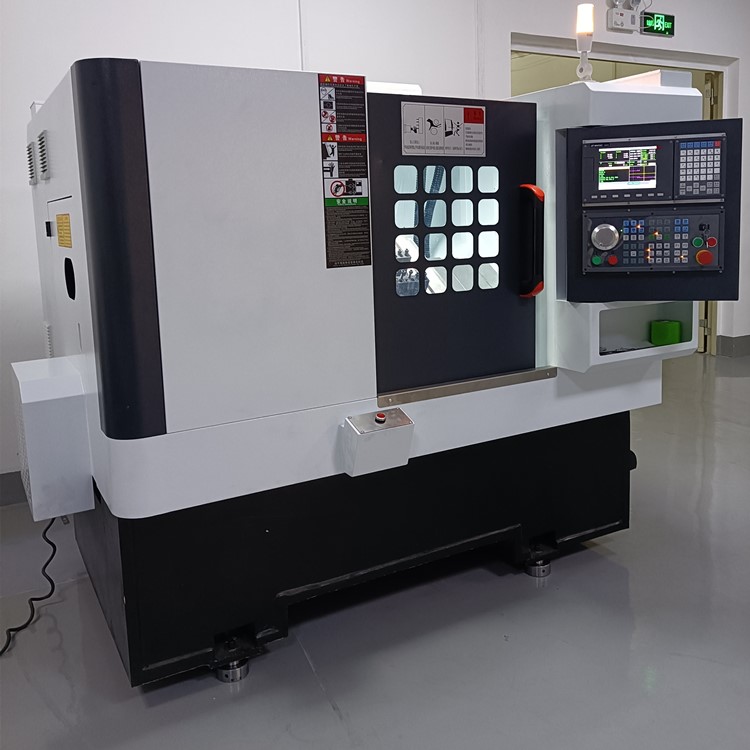
广东好的数控车床哪家质量好?
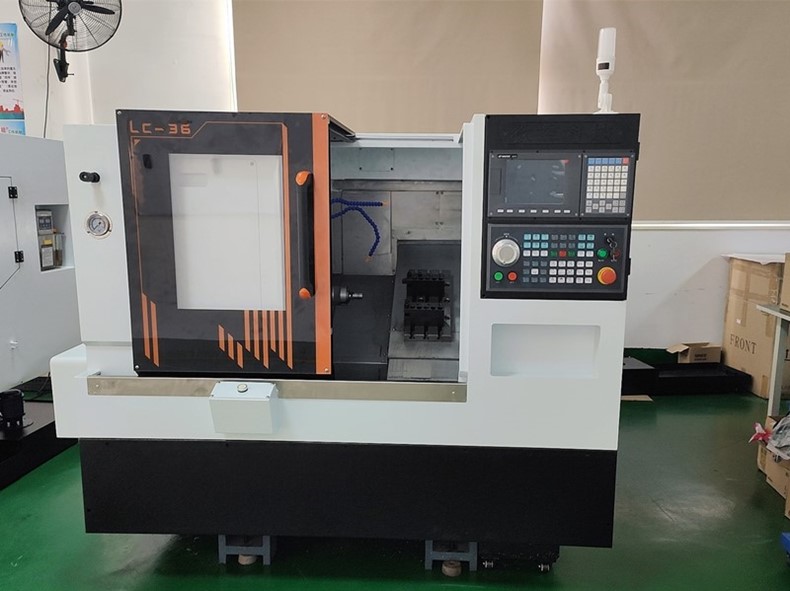
车铣复合数控机床多少钱?
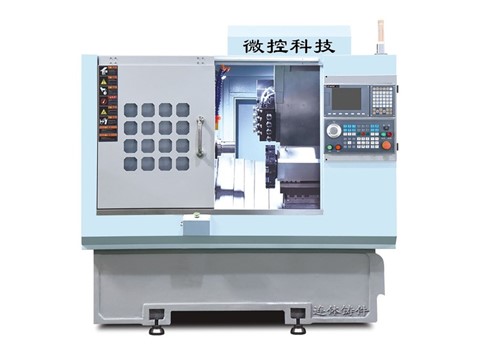
斜轨数控车床的结构特点
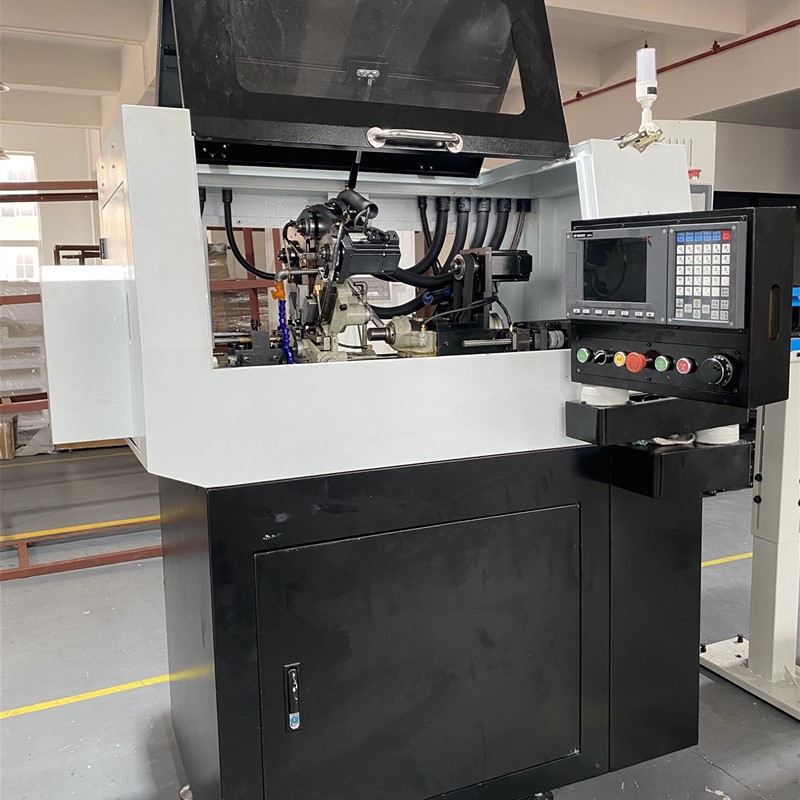
什么是数控凸轮走心机?
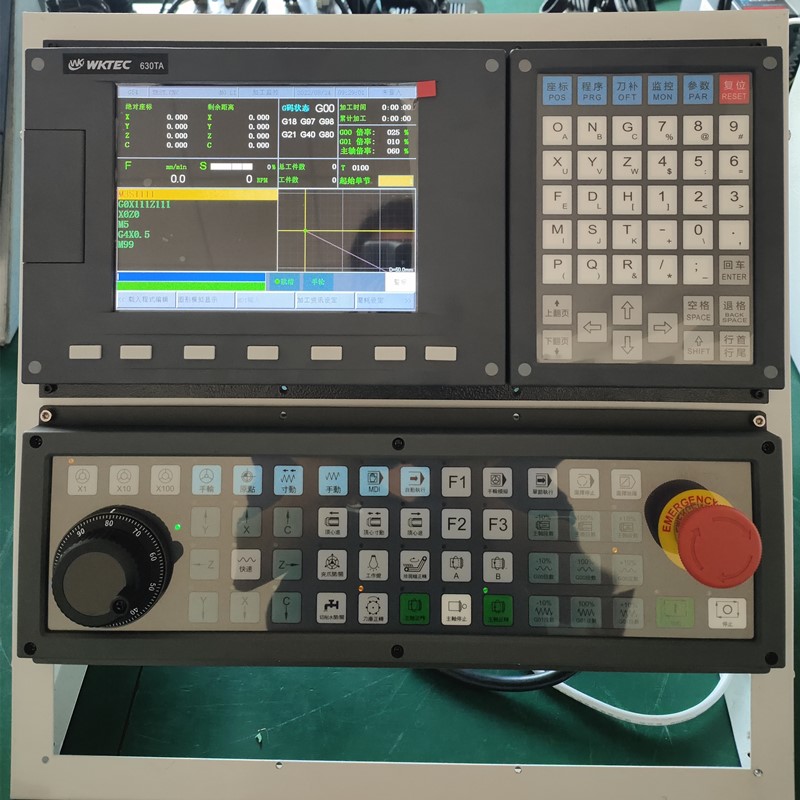
630TA多轴多通道数控系统
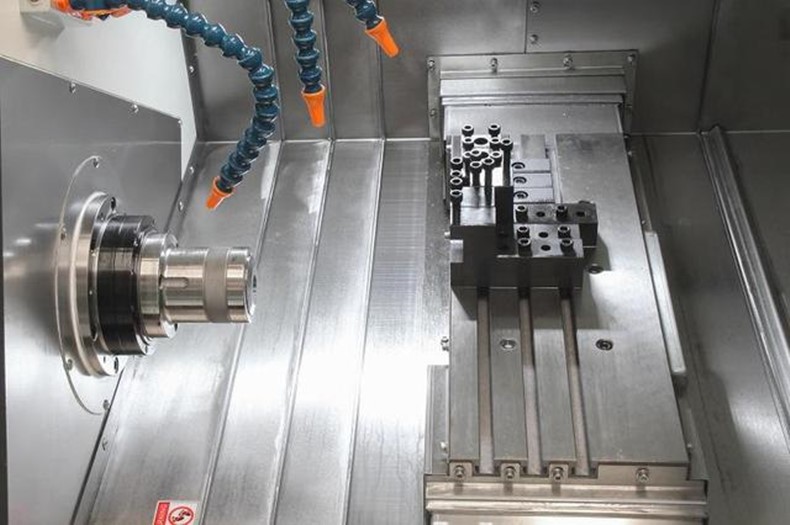
如何快速操作数控车床-数控车床编程的快捷键大全(下)